There are three terms that have relevance to carving and lapidary working of rocks and minerals, these are rock hardness, mineral hardness, and mineral fracture toughness. These three terms have different meanings and are often confused and interchanged in modern alternative literature on the subject of the carving and lapidary working of rocks and minerals by the ancient Egyptians.
a) Rock Hardness
b) Mineral Hardness
c) Mineral Fracture Toughness
a) Rock Hardness
Rock hardness is a term used in geology to denote the cohesiveness of a rock and is usually expressed as its compressive fracture strength. Terms such as hardrock and softrock are used by geologists to distinguishing between igneous/metamorphic and sedimentary rocks, respectively. These terms originated from historical mining terms, reflecting the methods needed to economically mine an ore deposit. For example, a hardrock needs to be mined with explosives and a softrock can be mined with hand tools, such as pick and shovel.
Rocks can be tested for their unconfined fracture strength by using ASTM standard tests. These involve loading a small rock core at a rate of 0.7 MPa/s until it fails brittlely. The fracture strength is given as the maximum stress necessary to induce failure of the rock core. This value gives an indication of the cohesiveness and density of a rock. As seen in Table 1 igneous, metamorphic and sedimentary rocks can be classified from very weak to very strong with regards to their unconfined fracture strengths (Attewell & Farmer 1976). Generally, sedimentary rocks can range from weak to medium (10-80 MPa), and igneous rocks range from medium to very strong (40-320 MPa). The highest unconfined compressive strength observed in a rock is on the order of 400 MPa (e.g. nephritic jade).
Table 1. Classification of rock hardnesses (from Attewell & Farmer 1976).
|
|
|
|
|
weathered and weakly-compacted sedimentary rocks |
|
|
weakly-cemented sedimentary rocks, schists |
|
|
competent sedimentary rocks; some low-density coarse-grained igneous rocks |
|
|
competent igneous rocks; some metamorphic rocks and fine-grained sandstones |
|
|
quartzites; dense fine-grained igneous rocks |
Table 2 presents the typical unconfined compressive, tensile, and shear strengths for a variety of rock types (Attewell & Farmer 1976). It can be seen that each rock type can exhibit considerable variation. These variations are the result of a number of factors, which include porosity, grain size, grain shape, grain and crystallographic preferred orientation, mineralogy, and moisture content. In most rocks the main factors controlling rock hardness are porosity, grain size, and grain shape. All three of these factors affect the surface area of the interlocking bond forces at mineral grain to grain contacts. In most rocks the higher the surface area of mineral grain to grain contact the harder the rock becomes, for example:
i) Decreasing porosity in rocks increases the surface area of grain contacts.
ii) Decreasing the size of mineral grains in the rock increases surface area of grain contacts.
iii) The surface area of equant or irregular grains is greater than that of angular grains.
Sedimentary rocks generally have high porosity, a reflection of the processes of their formation and the nature of the cementing agent. As a result they are generally low in rock hardness (Table 2), and their grains are less tightly held together. Fine-grained and lower porosity igneous rocks, such as basalt and diabase (dolerite) are generally higher in rock hardness than that of coarser grained igneous rocks, such as granite, diorite, and gabbro. As a result, the mineral grains of fine-grained igneous rocks are more tightly held together than that of coarse-grained igneous rocks. In metamorphic rocks, where strong foliations have developed, rock hardness is generally lower due to the preferred orientation of mineral grains and the structural weaknesses these impose. However, in low grade metamorphism where a foliation does not develop, but the rock became more indurated (i.e. more compacted and lower porosity), rock hardness increases. This is the case for the rock slate, which is the indurated metamorphic form of the sedimentary rock shale (Table 2). A list of the properties of some Egyptian building stones (Arnold 1991) are presented at the following website (Egyptian Building Stones and their Properties [1 kg/gcm=0.098 MPa]).
|
|
|
|
|
|
|
|
|
|
|
|
|
|
|
|
|
|
|
|
|
|
|
|
|
|
|
|
|
|
|
|
|
|
|
|
|
|
|
|
|
|
|
|
|
|
|
|
|
|
|
|
|
|
|
|
|
|
|
|
|
|
|
|
|
|
|
|
|
|
|
|
|
|
|
|
|
|
|
|
|
|
|
|
|
|
|
|
|
|
In carving and lapidary working of rock, rock hardness plays an important role in determining the rocks susceptibility to brittle failure during the working process. Rocks that have high hardnesses are less susceptible to fracturing, and their mineral grains are more tightly held and less likely to be plucked out of the rock’s surface while being worked. This means that hardrocks are more durable, can take on high polishes, and can be finely detailed when carved, three properties that make them ideal for high quality, finely detailed statuary (e.g. nephritic jade). However, this also makes them harder to carve, in the sense of more labor intensive and time consuming activity. Most hardrocks can be carved by percussion, which involves striking the rock surface with a hammer (Rich 1970). This causes fracturing or cleavage of the mineral grains on the surface of the rock (see fracture toughness below), and allows the rock to be shaped. The high fracture strengths of hardrocks minimizes the risk of significant fractures forming within the rock when sufficient impact stresses are applied to crush the mineral grains on the rock’s surface. Today, percussion carving is generally done with cast iron or soft tool steel Boucharde or bush hammers (Fig. 1). In modern percussion carving, hardrocks can be shaped to a fine scale by this method (Rich 1970).
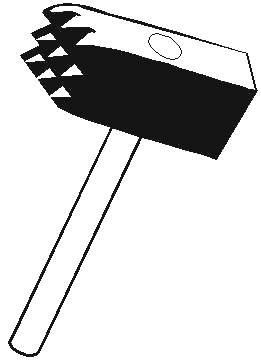
The ancient Egyptians did not have ready access to cast iron or steel for most of their history and would have used rock hammers, broad chisels, and punches (Zuber 1956, Stocks 1999; 2001). The rock hammer or stonemason’s maul only needs to have a rock hardness greater than the rock being carved. As a result the harder rock degrades less than the softer rock, allowing the surface of the softer rock to be mechanically broken down and the rock to be slowly shaped. As we see in Table 2, diabase (dolerite) can be harder than that of most other coarser grained igneous rocks, and as a result it make a good rock hammer. Egyptian quarries are littered with spherical diabase pounders (Klemm & Klemm 1993), examples of which can be seen from the Sphinx temple, as well as other places throughout Egypt (e.g. UC27323, UC35981, UC379, UC21411). Numerous tomb painting and reliefs have been found that demonstrate the use of stonemason’s maul in the making of stone statuary (Eaton-Krauss 1984). Figure 2 represents an image of 2 sculptors working with stonemason’s mauls in the tomb of Tjj from the Old Kingdom period. The stonemason’s maul would appear to be made of a blunt stone head (e.g. UC30858, UC30184, UC16328) connected by leather thongs to two wooden rods that were used as handles.
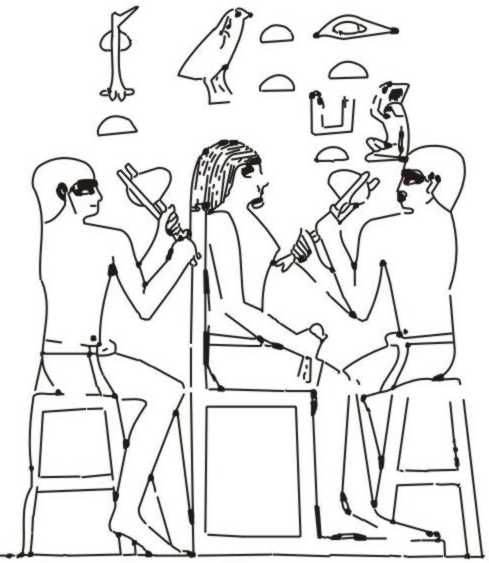
Softer sedimentary rocks can be carved with hardened copper and bronze chisels as well as with stone hammers (Stocks 1999). During lapidary working, less indurated softrocks are more susceptible to grain plucking because of their high porosity, which leads to their grains being less tightly held together. In many cases this prevents fine detail and high polish from being obtained in these rock types. More indurated sedimentary rock, such as metasedimentary rocks, are more ideal for fine carving because their grains are more tightly held together. As a result they can be worked with fine detail, highly polished, and thin sectioned with less risk of fracturing during the working process. An example of this is the metasiltstone cup from the tomb of Queen Her-nit (image) and the metasiltstone ornamental bowl from the tomb of Sabu (Fig.3, image), both are from the Early Dynastic period. Note that both the easy to which these rocks can be carved and their durability are taken to full advantage by the early Egyptian artisans.
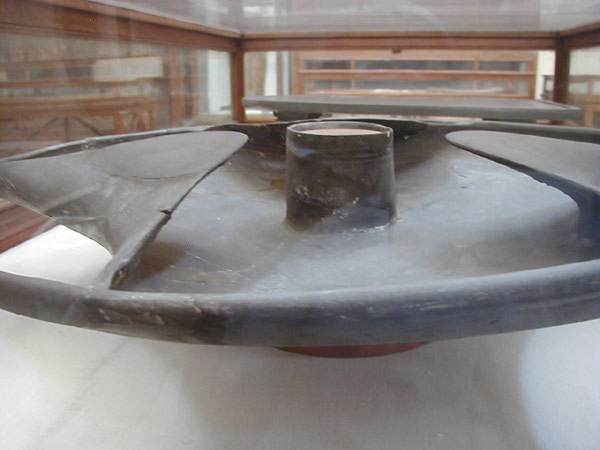
Fig. 3. Ornamental bowl from the 1st Dynasty tomb of Sabu (Tomb 3111). (d. 62 cm, Cairo Museum, Photograph by Jon Bodsworth The Egypt Archive).
b) Mineral Hardness
Hardness of a crystalline solid, with respect to abrasion, may mean one of two things:
i) The ability of one mineral to scratch or abrade another, this is called Mohs’ hardness.
ii) The resistance to indentation under a steadily applied stress, this is call indentation hardness or microhardness.
Each of these is a measure of a crystalline structure’s resistance to mechanical breakdown, which reflects the strength of atomic bond within the crystallographic lattice of a specific material.
Mohs’ scale of hardness represents a scale of relative mineral hardness rather than a scale of absolute mineral hardness. The key word here is “relative”… what this means is that Mohs’ scale is actually just an arbitrary list or table and does not represent the actual value of hardness. It is a list of 10 common minerals that increase in hardness as one ascends the list. As a result the scale cannot be used directly to qualitatively define the actual hardness of a mineral. It was originally designed by Fredrick Mohs in the early 19th century to be use in combination with a number of other diagnostic tests and observations for mineral identification by geologists and mineralogists (e.g. streak, cleavage, crystal habit, etc.). On Mohs’ scale a mineral will scratch another mineral of equal or lesser hardness than itself. This allows the 10 common minerals of Mohs’ scale to be used to make a simple scratch test to grade that an unknown mineral can scratch or be scratched by another, and in so giving a rough estimate of relative hardness. This test allows the unknown mineral’s relative hardness to be compared to a list of known relative mineral hardnesses to help in identification. As a result Mohs’ scale is usually graduated only to 0.5 or 0.25 intervals.
In order to compare absolute mineral hardnesses one must use other methods. For example, Vickers or Knoop microhardness, which are measures of indentation hardness. These methods requires a large expensive loading machine, a high powered research microscope, and time consuming specimen preparation to determine the actual hardness of a mineral. As a result, these testing methods are usually associated with engineering material labs. Microhardness is not generally used in geology (usually in combination with reflectivity studies to help in the identification of ore minerals), however, most geologist and lapidist know the general relationship between Mohs’ scale and microhardness (Table 3). Because of the anisotropy of indentation hardness with respect to crystallographic orientation and the limitation of the different microhardness testing methods, generally Knoop’s method is used to determine the indentation hardness of minerals. The shape of the Knoop’s die is such that it allows the testing of different crystallographic orientations and planes. The Knoop’s value is given as an average of different crystallographic orientations.
Mineral | Knoop | Vickers | Mohs’ |
Talc | NA | 1 | 1 |
Gypsum | 61 | 3 | 2 |
Calcite | 141 | 9 | 3 |
Fluorite | 181 | 21 | 4 |
Apatite | 483 | 48 | 5 |
Orthoclase | 621 | 72 | 6 |
Quartz | 788 | 100 | 7 |
Topaz | 1190 | 200 | 8 |
Corundum | 2200 | 400 | 9 |
Diamond | 8000 | 1600 | 10 |
Table 3. Mineral Hardnesses
The problem with Mohs’ scale is that natural diamond is extremely hard, as its value on the Knoop microhardness scale clearly shows (Table 3, Fig. 4a). When Mohs’ scale is plotted against the log of indentation hardness, minerals 2 to 9 on Mohs’ scale make an approximate linear relationship (Fig. 4b). On Knoop’s scale quartz is only about 10% the indentation hardness of natural diamond, which is considerable different from what one might expect if Mohs’ scale is taken literally. In actual fact minerals 1 to 9 on Mohs’ Scale are all less than 30% the indentation hardness of diamond. There is no known natural mineral with a hardness greater than 30% the hardness of diamond, but there are synthetic materials that are, such as silicon carbide and boron carbide. These are used as abrasives and are both less than 40-50% the hardness of natural diamond (Table 4).

Material | Knoop (kg/mm2) | Mohs’ |
Copper | 120 | 3 |
Copper (hammered) | 150-200 | 3.25-3.75 |
Bronze | 175 | 3.5 |
Cast Iron | 200-500 | 4-5 |
Steel | 400-600 | 5.5 |
Glass | 700 | 6-7 |
Hardened Steel | 700-1000 | 6.5-7.5 |
Aluminum oxide | 2000-2050 | 8-9 |
Tungsten Carbide | 2050-2150 | 9 |
Silicon carbide | 2150-2950 | 9-10 |
Boron carbide | 2900-3900 | 9-10 |
Synthetic Diamond | 6000-7500 | 10 |
Diamond | 8000-8500 | 10 |
Mineral hardness is the most important factor in the lapidary working of rocks and minerals. A mineral can be scratched by an abrasive of equal or greater hardness than itself. If this were not the case diamond could not be faceted and polished, since it is the hardest known substance. When abrasives are uses on rocks and minerals they are usually held against the surface with a lapping material. In quality lapidary working of rocks and minerals the lapping material is always less hard than the material being lapped and, therefore, the abrasive. This allows for the abrasive to penetrate into the softer lapping surface and be held there. It is only the abrasive that actually does the cutting not the lapping material, and it does this through the process of abrasion. Many materials can be used as a lapping surface, for example felt, canvas, leather, bone, wood, resin, copper, tin, bronze, iron, soft steel, and ceramics to name a few. The more durable the lapping surface the less it needs to be replaced. Copper is an ideal lapping surface and it holds abrasive very well, either loose on the surface of charged (impregnated into the metal). Today, 1/4″ thick cold-rolled copper disk laps charged with diamond abrasive can be used in the faceting of diamonds. Copper, as well as other metals, are used today in both drill bits and large-diameter core drilling of rocks and minerals by amateur lapidist (Sinkankas 1984). Copper is also used today for saw blades and lapidary carving tools (Long 1976).
The ancient Egyptians had access to copper, which could have been hardened by hammering to make it more durable (Lucas & Harris 1962). Copper can be cold-working by hammering to increase the hardness above its cast or fully annealed condition without cracking of the hardened edge (Desch 1927). It can actually be increased by more than a factor of 2, harder than annealed pure iron or low carbon steel (Wertime & Muhly 1980). Copper charged with quartz abrasive can cut quartz just as copper charged with diamond abrasive can cut diamond. For most of the history of ancient Egypt quartz was the hardest mineral that they worked to a large degree. Minerals such as garnet, which can be slightly harder than quartz (Mh. 7-7.5), were worked to a small degree. There is some evidence from the Predynastic period, that beryl (Mh. 7.5-8) was worked. During this time they appear to have drilled holes into beryl, so that unworked hexagonal crystals could be mounted in jewelry (Lucas & Harris 1962). Most likely they were using beryl as an abrasive. They did not appear to have the ability to work beryl to any major degree until the Ptolemaic period where corundum abrasive (similar in hardness to silicon carbide) was more readily available. An example of an ancient Egyptian lapidary cutting tool is presented in Figure 5 a-b (Hodges 1964) from an Old Kingdom period tomb (ca. 2500 BC). A reconstruction of the boring drill (Fig. 5b) consists of a weighted wooden handle and a crescent shaped flint (cryptocrystalline quartz) cutting head (e.g. UC6134, UC6135), and this type of cutting head was primarily used in the manufacturing of soft stone vessels made of gypsum (Stocks 1993) and steatite. In soft stones, tools like these would be used to both bore and hollow, starting with the initial neck hole extending to the bottom of the vase, which allows access to the interior for hollowing. In indurated and harder porous limestones, as well as igneous rocks, copper tube coring drills would be used to cut the center hole, this would then be followed by the insertion of a lapping tool and abrasive for interior hollowing (Stocks 1993). Circular ring marks are often observed on the bottom of stone vessels starting from the middle of the 1st dynasty onward, representing the depth of the coring barrel’s cut (Petrie c1977).
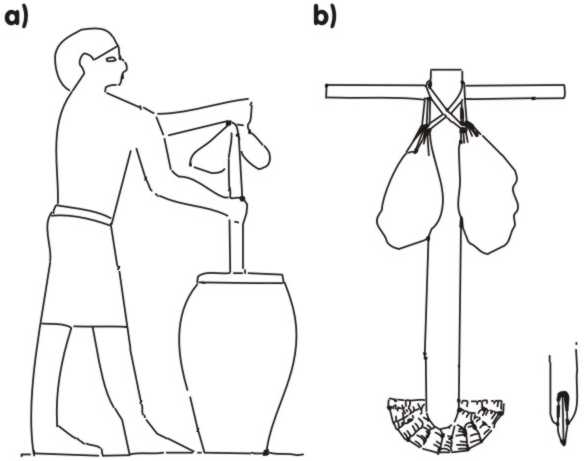
Although usually associated with minerals, in most cases Mohs’ hardness cannot be applied to rocks because of the variability of their mineral composition. However, there are two terms that associate Mohs’ scale with rocks in a lapidary and carving context. These terms are soft stone and hard stone. These are terms that are loosely associated with rocks that are monomineralic (i.e. mainly made up of one specific mineral). For example, rocks such as soapstone (talc), steatite (talc), alabaster (gypsum), and marble (calcite) are considered soft stones because their mineral grains have hardnesses that are quite low and can be carved by a single abrasive stroke. Rocks such are jade (nephrite, jadeite varieties), anorthosite (feldspar), quartzite (quartz) are considered hard stones since their mineral constituents have high indentation hardnesses and must be carved by continuous abrasion or lapping.
Quartz vs. quartz abrasion
To test that quartz can be used to cut quartz, a specimen of quartz was obtained and a small simple scribing tool was made. The specimen (Fig. 6a) is from a 10 cm intergrown quartz crystal (amethyst) from a vein located in the Thunder Bay region, Ontario, Canada (McArthur et al. 1993). The specimen is mounted with epoxy in a polished section casing and has been thick sectioned (top has been sawn off), so the surface is unpolished but smooth (very minor saw striations). The c-axis of the quartz crystal is orientated approximately vertically in the plane of the image. All images were scanned with a HP4100c or HP3300c flatbed scanner at 500dpi and in colour; a sheet of acetate was placed over the surface of the scanner for protection of the glass surface.
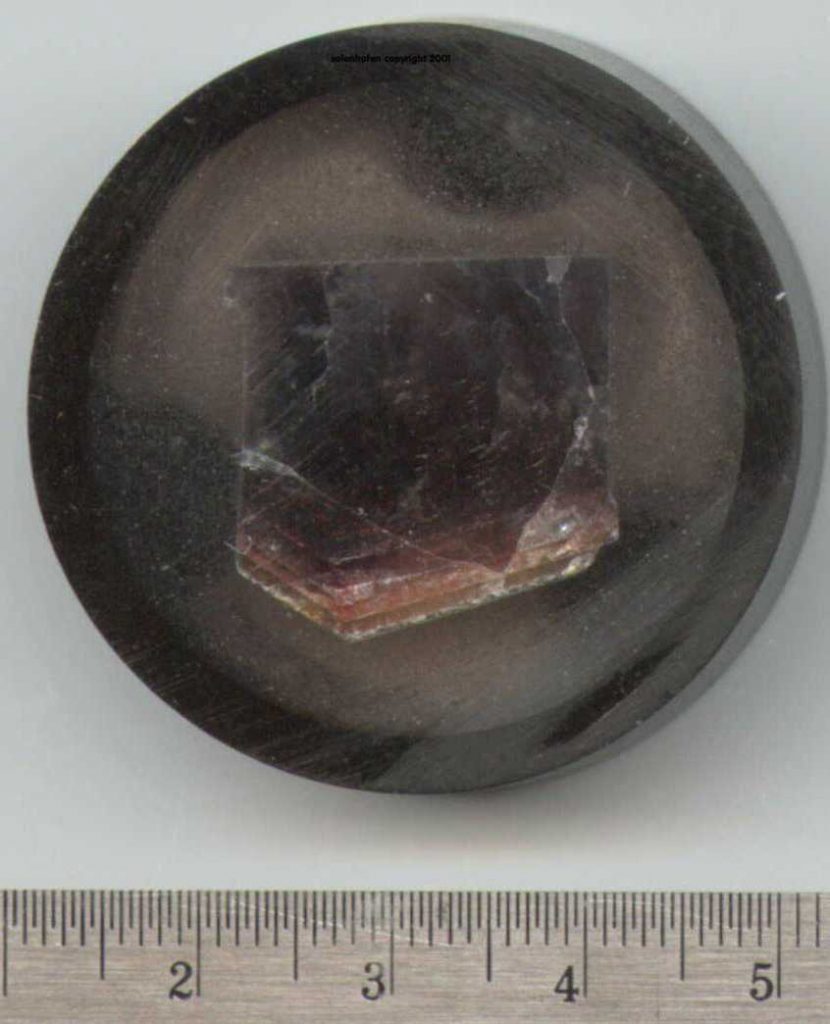
(scale in cm graduated to 0.5 mm)
A small specimen of quartz was crushed with a hammer and wedges of clear quartz were obtained for the head of the scribing tool. Milky looking quartz, indicating fractures and other structural weaknesses, was avoided. The pointed end of a round wooden toothpick (d. 2 mm) was sanded off and a razor saw was used to cut a 3-4 mm long groove in the end. The wedge of quartz was pushed into the groove and the end was wrapped in coarse thread and cemented with gap-filling cyanoacrylate glue. About 1.5 to 2 mm of quartz extended from the tip of the toothpick. Four of these scribing tools were made. A mechanical drafting pencil was used as a handle for these quartz scribing tools (fig. 6b).
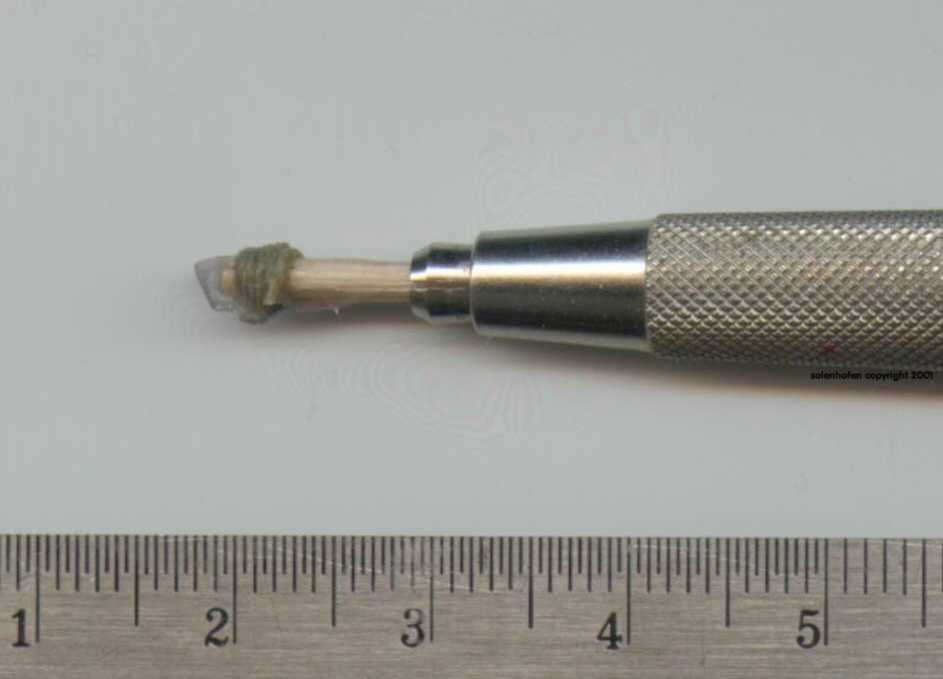
Grinding consisted of moving the scribing tool back and forth along the quartz surface at a 30-40ºangle from the perpendicular. To start, a metal ruler was glued to the section of quartz to be used as a guide, but was later remove once the depth of the groove was sufficient to hold the scribing tool in line. The shear stress exerted on the scribing tool was by hand alone and was low, certainly less than that necessary to break a wooden toothpick. The speed of grinding was about 3-4 strokes per second and was conducted for twelve 5 min intervals or 1 nonconsecutive hour. About 50% of the grinding time was done under wet conditions using water and the remaining time was under dry conditions. The wet and dry grinding did not appear to make much of a difference other than the sound generated during grinding was considerably less when water was used. All four of the scribing tools were used, and two of the quartz wedges broke on the first few initial strokes, most likely the result of microfractures. Of the other 2 used, the quartz scribing head of one was worn down to nearly the end of the wooden toothpick and the other about a third of the way.
The results of this experiment can be seen in Figure 6c which clearly shows a 2 cm long groove cutting horizontally across the quartz specimen. A visual inspection was made of the surface of the quartz specimen with a 10x jewelers loupe. From this it would be estimated that the horizontal groove is about 1 mm in width with a depth of about 0.3 to 0.5 mm. The surface of the groove is smooth and polished and has a rounded shape. The edges of the groove are quite crisp and show no sign of chipping, except were the groove crosses a crystal boundary on the far right side of the specimen.
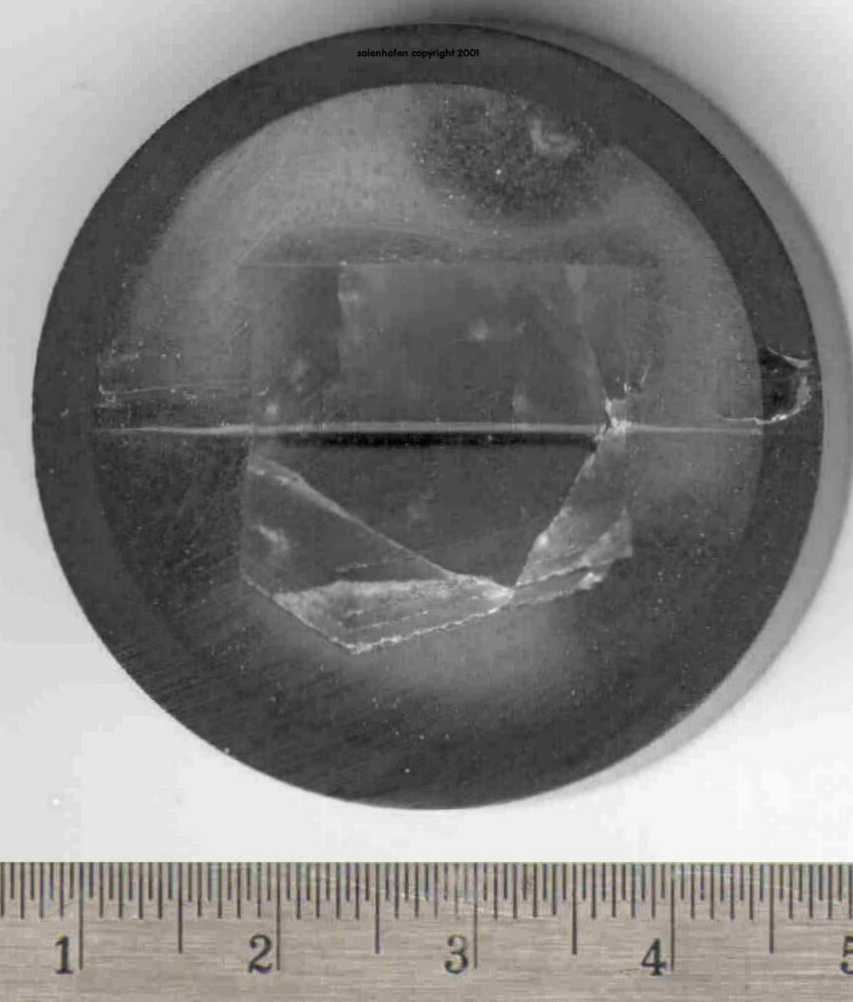
From this it becomes clear how quartz can be shaped with quartz abrasive. In this experiment a cutting rate of about 1 cm per day could be obtained using minimal pressure. In this case the pressure was insufficient to break a round wooden toothpick. One can certainly imagine that with increasing pressure the rate of cutting can be dramatically improved. The ancient Egyptians using cooper saws, drills, and laps should have no problem cutting quartz with quartz abrasive, not to mention all the other softer minerals they worked (which are many).
Quartz vs. hard modern metal
To test the ability to scratch quartz with a modern metal with a greater indentation hardness than quartz, a tungsten carbide pen scriber was used. The specimen (Fig 7a) is from the same deposit of quartz crystals (amethyst) mentioned above. The tungsten carbide scriber is seen in Figure 7b. The specimen is mounted with epoxy in a polished section casing and has been thick sectioned (top has been sawn off), so the surface is unpolished but smooth (minor saw striations). The images were scanned with a HP4100c and HP3300c flatbed scanner at 500dpi and in colour and BW; a sheet of acetate was placed over the glass surface of the scanner for protection of the glass surface.

Tungsten carbide has an indentation hardness very similar to the mineral corundum (Table 3 and 4) and a fracture toughness about 2-3x that of corundum (Table 5). Compared to quartz tungsten carbide is about 3 times harder and has a fracture toughness about 3-4 times higher. Tungsten carbide has no problem scratching quartz in a single stroke.
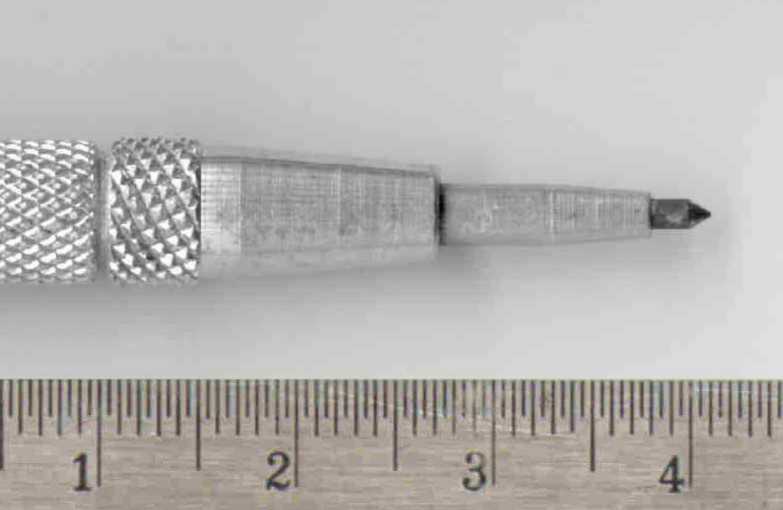
The quartz specimen was scribed 6 times with single strokes moving from left to right holding the pen at about 30º from perpendicular in the plane of the scribing stroke. The grooves are all very noticeable when wetted and seen in reflected light and can be seen in Figure 7c. The top 4 horizontal single stroke scratches were made with pressure exerted from hand and arm alone by dragging the scriber across the surface using a metal ruler as a guild. The bottom two single stroke scratches were made with pressure from weight of the my upper torso and a metal ruler was again used. The pressure exerted increases from very little in the case of the top line to moderate on the bottom line. In Figure 8 another specimen was used and a high moderate force was applied, but no ruler was used. The magnitude of the force was restricted by the difficulty of holding a 4 cm diameter polish section casing and ruler in one hand and the application of a forceful scribing stroke with the other. After the scribing was completed the surface of the specimens were cleaned of debris with water and a fine copper brush.
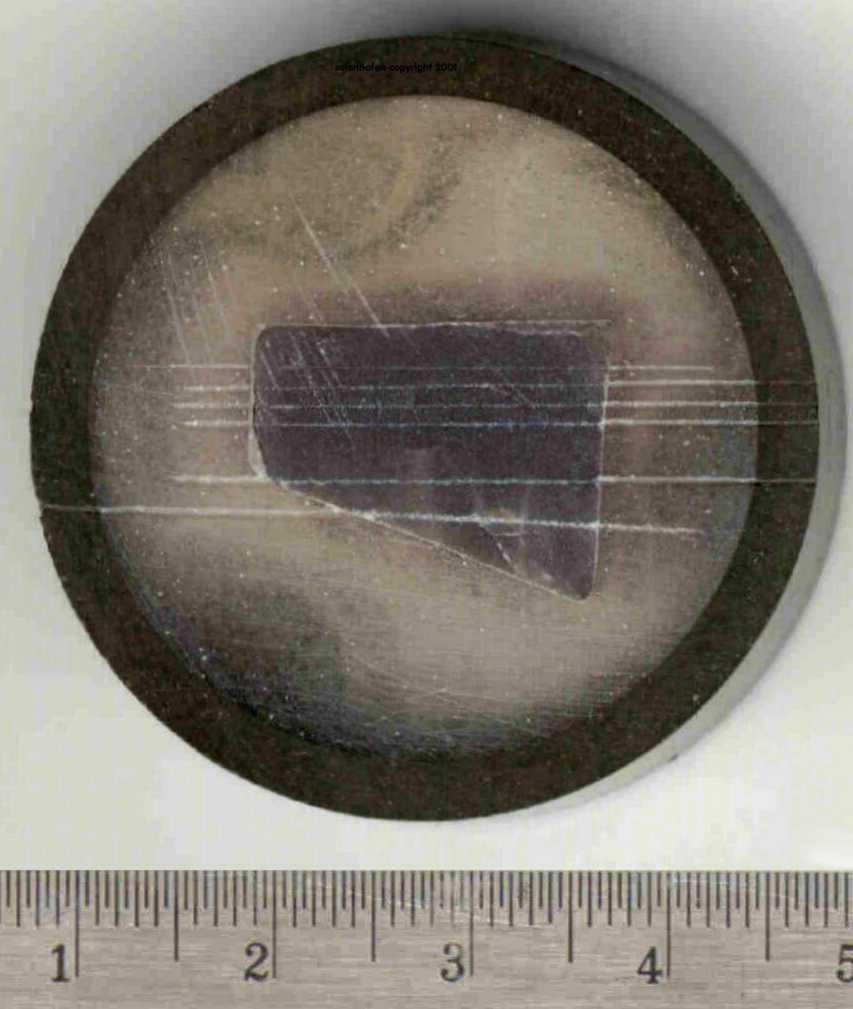
Although the depth of the scratches cannot be clearly seen in the above image a visual inspection of the surface was made with a 10x jewelers loupe. From this an estimate of the 6 horizontal scratches can be made in Figure 7c. Starting from the top to bottom the lines range from about 0.05 to 0.25 mm in width with a depths less than and up to about 0.075 mm. The scribed lines are quite crisp and show little chipping and pitting of the quartz on the lines edges, but do show some pitting on the bottom surface. The scratch in Figure 8 is about 0.35 to 0.4 mm in width and 0.10 to 0.15 mm in depth. This scribed line shows some pitting and chipping of the quartz.
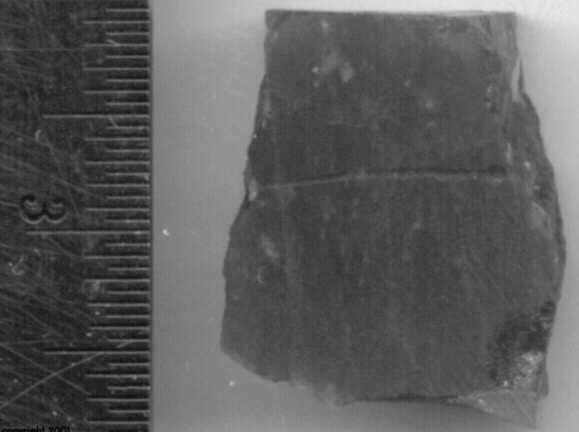
c) Mineral Fracture Toughness
Mineral toughness is defined as a qualitative value that represents a minerals resistance to fracture when exposed to a high strain rate impact stress. Mineral toughness is different from mineral hardness, for example some minerals that have high indentation hardnesses are fragile. They chip and fracture easily and require care when being worked to minimize potential damage. Topaz is an example of such a mineral, with an indentation hardness twice that of quartz, but also very susceptible to fracturing. Other minerals of lower hardness are less susceptible to fracturing and are ideal for lapidary carving and the making of thin-rock sections. An example of such a mineral is nephrite (jade), which is the 2nd toughest naturally occurring mineral with an indentation hardness similar to that of feldspar. The fracture toughness of minerals are measured with a Charpy V-notch testing apparatus and in units of MPa(m)1/2. Minerals can be graded in terms of their fracture toughness from poor, fair, good, excellent, and exceptional. Table 5 lists these grades for common minerals as well as some other misc. materials.
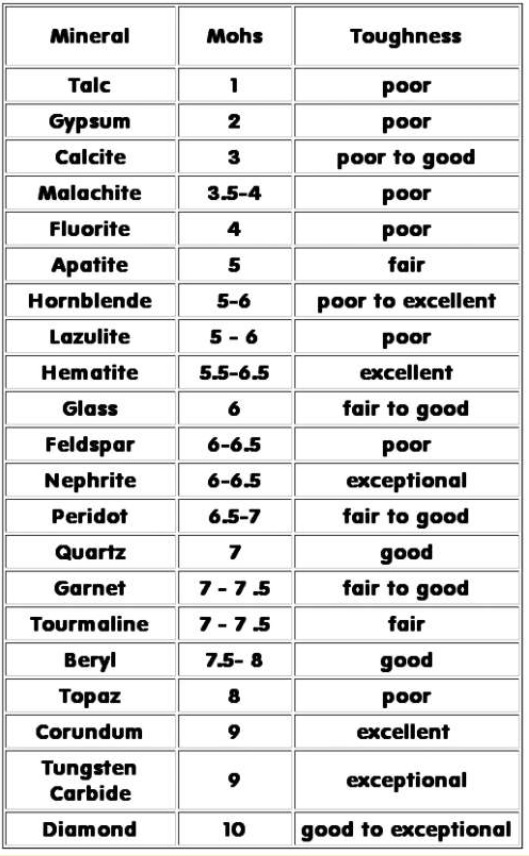
The gradings listed in Table 5 are of particular importance in understanding how the Egyptians carved hardrocks. We know that many of the hardrocks used by the ancient Egyptians were feldspar rich (e.g. granite and granodiorites from Aswan, anorthosite and diorite gneisses from Chephren’s quarry). From Table 6 it can be seen that feldspar in a very brittle mineral and highly susceptible to fracture upon impact. The reason why feldspar is so susceptible to impact stresses is because of the fact that it has 2 good cleavage planes. Impacting the surface of an anorthosite or diorite leads to carving of the frontal or cubic stylization that are associated with it, for example Khafre’s diorite gneiss statue at the Cairo museum (Fig 9).
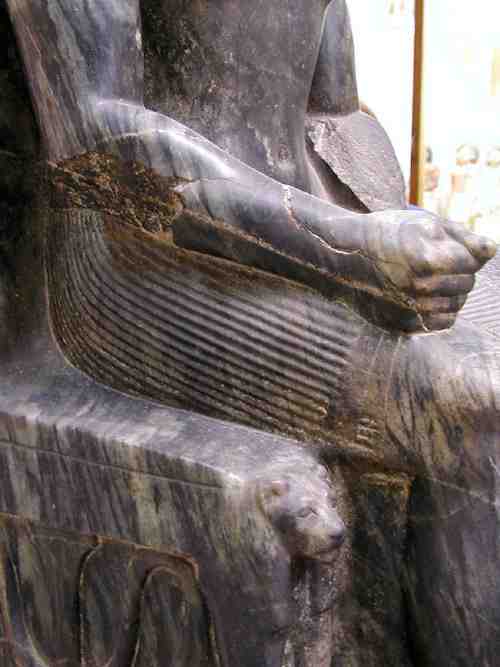
References and Bibliography
Aldred, C. (1965) Egypt to the end of the Old Kingdom. McGraw-Hill, New York, 143 p.
Attewell, P.B. and Farmer, I..W. (1976) Principles of engineering geology. Chapman and Hall, London, 1045 p.
Arnold, D. (1991) Building in Egypt: pharaonic stone masonry. Oxford University Press, New York, 316 p.
Bloss, F.D. (1971) Crystallography and crystal chemistry: An introduction. Holt, Rinehart and Winston, New York, 554 p.
Desch, C.H. (1927) The tempering of copper. Discovery, 8, 361-362.
Eaton-Krauss, M. (1984) The representations of statuary in private tombs of the Old Kingdom. Otto Harrassowitz, Wiesbaden, 208 p.
Eliscu, F. (1959) Sculpture: techniques in clay, wax, slate. Chilton Book, Philadelphia, 192 p.
Eliscu, F. (1972) Slate and soft stone sculpture. Chilton Book, Philadelphia, 145 p.
Emery, W.B. (1949) Great Tombs of the First Dynasty: Excavations at Saqqara v.1. Goverment Press, Cairo, 157 p.
Emery, W.B. (1961) Archaic Egypt. Penguin Books, Harmondsworth, 269 p.
Hodges, H.W.M. (1964) Artifacts: an introduction to primitive technology. F.A. Praeger, New York, 248 p.
Klemm, R. and Klemm, D.D. (1993) Steine und steinbrüche im alten Ägypten. Spring-Verlag, Berlin, 465 p.
Long, F.W. (1976) The creative lapidary: materials, tools, techniques, design. Van Nostrand Reinhold, New York, 136 p.
Lucas, A. & Harris, J.R. (1962) Ancient Egyptian materials and industries. E. Arnold, London, 523 p.
Marks, M.K. (1963) Slate sculpturing. Dial Press, New York, 44 p.
McArthur, J.R., Jennings, E.J., Kissin, S.A., and Sherlock, R.L. (1993) Stable-isotope, fluid-inclusions, and mineralogical studies relating to the genesis of amethyst, Thunder Bay Amethyst Mine, Ontario. Canadian Journal of Earth Science, 30, 1955-1969.
Penny, N. (1993) The materials of sculpture. Yale University Press, New Haven, 318 p.
Petrie, W.M.F. (c1977) The funeral furniture of Egypt: with stone and metal vases. Aris & Phillips, Wiltshire. 65 p.
Rich, J.C. (1970) The materials and methods of sculpture. Oxford Univ., New York, 416 p.
Scarfe, H. (1975) The lapidary manual. B.T. Batsford, London, 172 p.
Shelley, D. (1993) Igneous and metamorphic rocks under the microscope: classification, textures, microstructures and mineral preferred-orientations. Chapman & Hall, New York, 445 p.
Sinkankas, J. (1984) Gem cutting: a lapidary’s manual. Van Nostrand Reinhold, New York, 365 p.
Stocks, D.A. (1993), Making stone vessels in ancient Mesopotamia and Egypt. Antiquity, 67, 596-603.
Stocks, D.A. (1999) Stone sarcophagus manufacture in ancient Egypt. Antiquity, 73, 918-22.
Stocks, D.A. (2001) Testing ancient Egyptian granite-working methods in Aswan. Upper Egypt. Antiquity, 75, 89-94.
Thornton, P.A. and Colcngelo, V.J. (1985) Fundamentals of engineering materials. Prentice-Hall, Englewood Cliffs, 679 p.
Wainwright, J. (1971) Discovery of lapidary work. Mills & Boon, London, 216 p.
Wertime, T.A. and Muhly, J.D. (1980) The coming of the age of iron. Yale University Press, New Haven, 555 p.
Zoltai, T. and Stout, J.H. (1984) Mineralogy: Concepts and principles. Burgess Publishing, Minneapolis, 505 p.
Zuber, A. (1956) Techniques du travail des pierres dures dans l’Ancienne Égypte. Techniques et Civilisations, 29-30, 161-180, 195-215.
References and Bibliography
Aldred, C. (1965) Egypt to the end of the Old Kingdom. McGraw-Hill, New York, 143 p.
Attewell, P.B. and Farmer, I..W. (1976) Principles of engineering geology. Chapman and Hall, London, 1045 p.
Arnold, D. (1991) Building in Egypt: pharaonic stone masonry. Oxford University Press, New York, 316 p.
Bloss, F.D. (1971) Crystallography and crystal chemistry: An introduction. Holt, Rinehart and Winston, New York, 554 p.
Desch, C.H. (1927) The tempering of copper. Discovery, 8, 361-362.
Eaton-Krauss, M. (1984) The representations of statuary in private tombs of the Old Kingdom. Otto Harrassowitz, Wiesbaden, 208 p.
Eliscu, F. (1959) Sculpture: techniques in clay, wax, slate. Chilton Book, Philadelphia, 192 p.
Eliscu, F. (1972) Slate and soft stone sculpture. Chilton Book, Philadelphia, 145 p.
Emery, W.B. (1949) Great Tombs of the First Dynasty: Excavations at Saqqara v.1. Goverment Press, Cairo, 157 p.
Emery, W.B. (1961) Archaic Egypt. Penguin Books, Harmondsworth, 269 p.
Hodges, H.W.M. (1964) Artifacts: an introduction to primitive technology. F.A. Praeger, New York, 248 p.
Klemm, R. and Klemm, D.D. (1993) Steine und steinbrüche im alten Ägypten. Spring-Verlag, Berlin, 465 p.
Long, F.W. (1976) The creative lapidary: materials, tools, techniques, design. Van Nostrand Reinhold, New York, 136 p.
Lucas, A. & Harris, J.R. (1962) Ancient Egyptian materials and industries. E. Arnold, London, 523 p.
Marks, M.K. (1963) Slate sculpturing. Dial Press, New York, 44 p.
McArthur, J.R., Jennings, E.J., Kissin, S.A., and Sherlock, R.L. (1993) Stable-isotope, fluid-inclusions, and mineralogical studies relating to the genesis of amethyst, Thunder Bay Amethyst Mine, Ontario. Canadian Journal of Earth Science, 30, 1955-1969.
Penny, N. (1993) The materials of sculpture. Yale University Press, New Haven, 318 p.
Petrie, W.M.F. (c1977) The funeral furniture of Egypt: with stone and metal vases. Aris & Phillips, Wiltshire. 65 p.
Rich, J.C. (1970) The materials and methods of sculpture. Oxford Univ., New York, 416 p.
Scarfe, H. (1975) The lapidary manual. B.T. Batsford, London, 172 p.
Shelley, D. (1993) Igneous and metamorphic rocks under the microscope: classification, textures, microstructures and mineral preferred-orientations. Chapman & Hall, New York, 445 p.
Sinkankas, J. (1984) Gem cutting: a lapidary’s manual. Van Nostrand Reinhold, New York, 365 p.
Stocks, D.A. (1993), Making stone vessels in ancient Mesopotamia and Egypt. Antiquity, 67, 596-603.
Stocks, D.A. (1999) Stone sarcophagus manufacture in ancient Egypt. Antiquity, 73, 918-22.
Stocks, D.A. (2001) Testing ancient Egyptian granite-working methods in Aswan. Upper Egypt. Antiquity, 75, 89-94.
Thornton, P.A. and Colcngelo, V.J. (1985) Fundamentals of engineering materials. Prentice-Hall, Englewood Cliffs, 679 p.
Wainwright, J. (1971) Discovery of lapidary work. Mills & Boon, London, 216 p.
Wertime, T.A. and Muhly, J.D. (1980) The coming of the age of iron. Yale University Press, New Haven, 555 p.
Zoltai, T. and Stout, J.H. (1984) Mineralogy: Concepts and principles. Burgess Publishing, Minneapolis, 505 p.
Zuber, A. (1956) Techniques du travail des pierres dures dans l’Ancienne Égypte. Techniques et Civilisations, 29-30, 161-180, 195-215.
Links
Ancient Egyptian Stone Technology
Findstone.com Marketplace for building stones
The Egypt Archive Jon Bodsworth’s image archive of ancient Egyptian antiquities